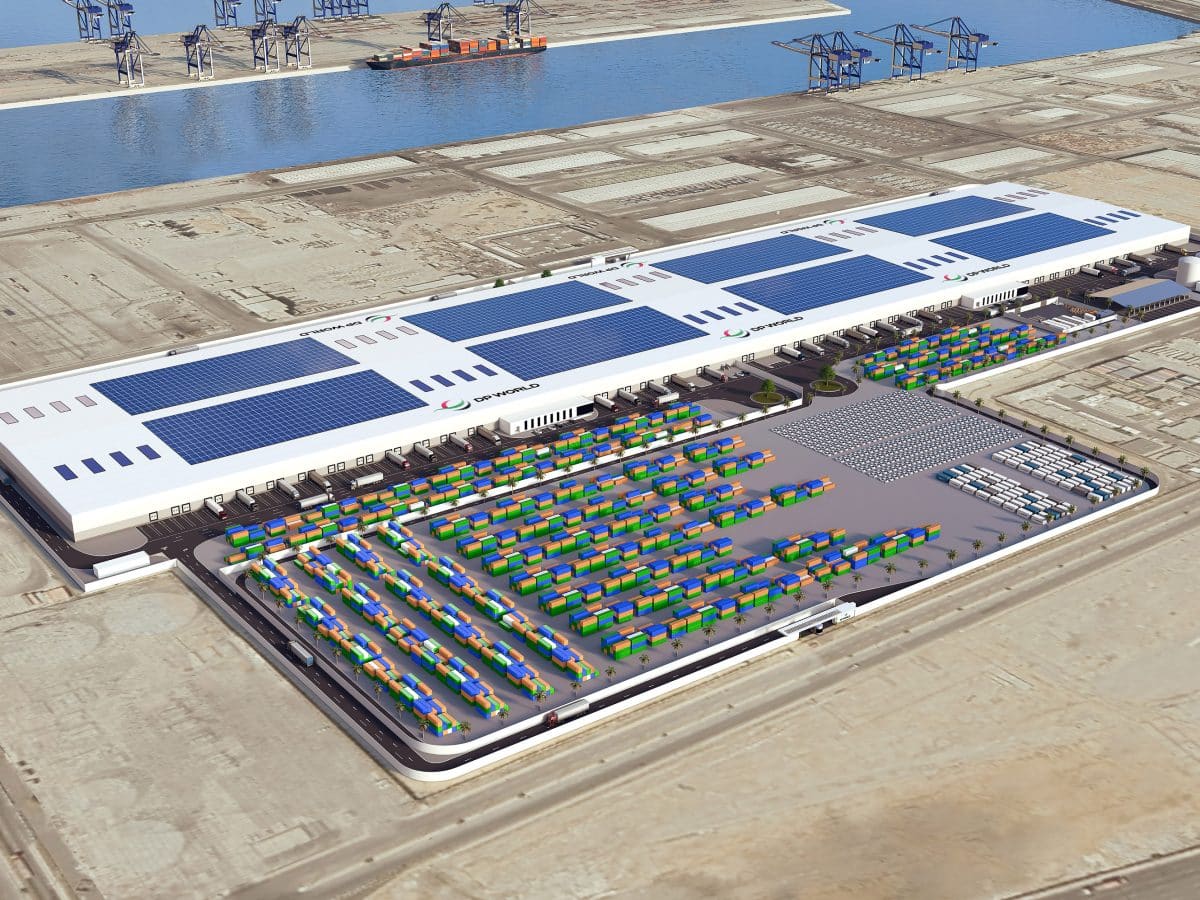
DP World and Saudi Ports Authority joint venture for Mega-logistics parks to transform logistics landscape in the Middle East
JEDDAH : The logistics landscape in the Middle East is undergoing a transformative shift with the recent commencement of a $250 million logistics park at Jeddah Islamic Port. The state-of-the-art facility, a joint venture between DP World and the Saudi Ports Authority (Mawani), is poised to become a cornerstone in regional trade, promising to enhance efficiency and streamline operations significantly.
As the largest integrated logistics park in Saudi Arabia, it exemplifies the potential of mega-logistics parks to revolutionise trade dynamics and bolster economic growth.
The concept of mega-logistics parks
Mega-logistics parks are expansive industrial zones meticulously designed to cater to the multifaceted needs of modern logistics. They serve as pivotal hubs for storing, managing, distributing, and transporting goods, significantly streamlining supply chain operations. These parks integrate advanced infrastructure and technology, providing a centralised ecosystem that enhances efficiency and reduces operational costs.
Mega-logistics parks fulfil several critical functions. They offer ample warehouse space for storing goods, sorting products, and managing fulfilment operations. These parks are designed to maximise productivity by clustering equipment and services required for outbound shipping. Ideally situated near significant seaports, airports, and railways, logistics parks also provide easy access to multiple modes of transportation. This connectivity reduces transportation costs and improves distribution efficiency.
Mega-logistics parks offer extensive and diverse warehousing options, including bonded and unbonded zones and dry, chilled, and cold storage facilities. These facilities support various logistics activities, from storage to light manufacturing and assembly.
These parks have state-of-the-art technology, such as automated storage and retrieval systems, advanced inventory management systems, and digital loading docks. This technological integration enhances operational efficiency and reduces labour costs.
Modern logistics parks increasingly incorporate sustainable practices. Features such as solar panels, energy-efficient LED lighting, and water recycling systems help reduce the environmental impact. Sustainable logistics parks also aim to minimise carbon emissions and energy consumption, aligning with global sustainability goals.
Beyond storage and distribution, many logistics parks offer additional services like product customisation, packaging, and assembly. These value-added services help companies streamline their supply chains and offer more personalised products to customers.
Case study: Jeddah Islamic Port Logistics Park
The Jeddah Islamic Port logistics park spans 415,000 square metres and will be developed in two phases, with an anticipated opening in Q2 2025. This facility is set to become the largest integrated logistics park in Saudi Arabia, offering 185,000 square metres of warehouse space, including bonded and unbonded zones and comprehensive dry, chilled, and cold storage facilities.
Strategically located along the vital Asia-Europe shipping route, the logistics park is designed to enhance multimodal connectivity. It is adjacent to DP World’s South Container Terminal, which is undergoing a comprehensive modernisation project to increase its handling capacity to five million twenty-foot equivalent units (TEUs) by Q4 2024.
The logistics park’s location facilitates efficient storage and distribution and provides seamless connectivity for importers and exporters, thereby streamlining supply chain operations. This strategic placement is expected to significantly boost the port’s capacity to handle increased trade volumes and reduce logistical bottlenecks.
The Jeddah logistics park is poised to deliver numerous benefits. The park will improve the speed and efficiency of goods movement by providing an integrated platform for logistics operations. This includes linking port operations with last-mile activities and offering import and export consolidation centres. The facility will also feature a rooftop solar plant generating 20 MW of renewable energy, underscoring its commitment to sustainability and reducing its carbon footprint. Moreover, with a capacity for over 390,000 pallet positions, the park is designed to accommodate significant trade volumes, ensuring scalability to meet future demand.
The development of the Jeddah logistics park aligns closely with Saudi Arabia’s Vision 2030, which aims to transform the Kingdom into a global logistics hub. The project supports the National Transport and Logistics Strategy by expanding the number of logistics centres in Saudi ports and fostering partnerships with major international logistics companies.
Comparative case studies
To illustrate the transformative impact of mega-logistics parks, we examine several successful examples worldwide. These case studies highlight the significant benefits that integrated logistics parks can bring to supply chain efficiency, cost reduction, and sustainability.
The Alliance Global Logistics Hub in Fort Worth, Texas, is a prime example of a successful multimodal logistics park. Established in the late 1980s and early 1990s through a unique public-private partnership, this hub combines rail, trucking, and air freight facilities. The hub’s development was driven by the need to create jobs and diversify the local economy following the collapse of the oil and gas industries. The presence of the Fort Worth Alliance Airport and a high-capacity roadway network has facilitated the efficient movement of goods, significantly reducing congestion and improving transportation efficiency.
India’s initiative to develop 35 Multimodal Logistics Parks (MMLPs) is part of its broader strategy to enhance logistics efficiency and reduce costs. These parks integrate various modes of transportation—land, sea, rail, and air—under one logistics operator, enabling seamless movement of goods. The strategic locations near key industrial and consumption centres help consolidate and distribute freight more efficiently. For instance, the MMLPs have helped lower transportation costs and reduce transit times, enhancing trade competitiveness.
Ocean Spray’s logistics initiatives showcase the benefits of distribution network redesign and intermodal transportation shifts. By shifting from road to rail for its New Jersey to Florida shipments, Ocean Spray achieved a 65% reduction in emissions and a 40% saving in transportation costs. Additionally, redesigning its distribution network to optimise the use of new facilities in Florida resulted in significant operational efficiencies and reduced carbon emissions.
DHL has implemented successful multimodal logistics solutions integrating air, sea, and land transportation. One notable example is the partnership with Schneider Electric, which developed a multimodal shipping model using Sustainable Aviation Fuel (SAF). This initiative reduced carbon emissions by 20% while optimising delivery times. Such integrated solutions highlight the importance of combining various transportation modes for cost savings and environmental benefits.
Commencing the $250 million logistics park at Jeddah Islamic Port marks a significant milestone in the Middle East’s logistics landscape. This state-of-the-art facility embodies the transformative potential of mega-logistics parks. By integrating advanced infrastructure, multimodal connectivity, and sustainable practices, the Jeddah logistics park is poised to revolutionise trade dynamics, enhance supply chain efficiency, and support Saudi Arabia’s ambitious Vision 2030 goals.