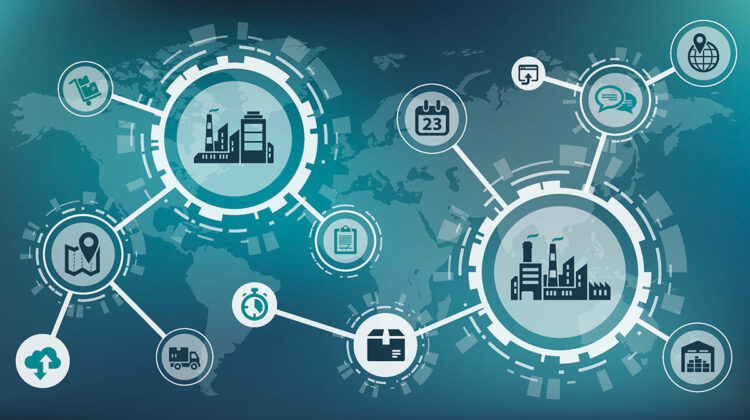
5 Ways Supply Chains Must Change To Prevent Future Christmas Shortages : Chairman & CEO, DP World
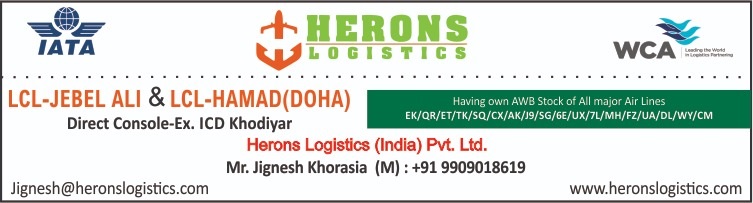
DUBAI : How did supply chains go from obscurity outside the industry, to being a topic of conversation at dinner parties in the space of a year? What started as a concern within the logistics industry is now impacting millions of businesses and consumers. Everything from petrol, children’s toys and Christmas decorations to new cars, chicken and lumber are being found in short supply in different parts of the world. In the run-up to the biggest retail period of the year, broken supply chains are headline news.
While it’s fair to say that the current disruption is largely due to the pandemic, I believe COVID-19 simply exposed a lack of resilience and structural weaknesses in the global supply chain.
In simple terms, the current shortages are a result of factory and warehouse shutdowns during the worst of the pandemic; truck driver shortages exacerbated by delays to licensing during lockdowns and unprecedented retirement levels; and new shutdowns now taking place in China and Vietnam due to the global gas crunch.
However, the real picture is more complex and it’s unlikely the disruption will be fixed in time for the Christmas rush. I believe it will continue until 2023.
Here are five changes that will help fix the global supply chain:
1. More global manufacturing hubs
COVID-19 has taught us that the global supply chain is far too reliant on China. Factory shutdowns there in 2020 continue to have an impact on product availability . A more diverse geographical spread of manufacturing hubs is critical to improve supply chain resilience. Although some companies have started to relocate manufacturing in other Asian countries such as Vietnam, this trend needs to accelerate rapidly and expand to create major manufacturing hubs outside of Asia-Pacific.
2. More regional logistics hubs
A wider geographical spread of manufacturing capacity will only happen if there is the supply chain infrastructure to support it. This includes greater access to regional logistics hubs. These hubs connect “remote” manufacturers to larger logistics networks, opening up more trade routes. Regional logistics hubs also help trade flow to new markets by taking in large shipments and separating them into containerised cargo that can be loaded straight onto a new ship bound for smaller markets. This is something we are doing at our Caucedo port and economic zone as we aim to turn it into the primary logistics hub for the whole of the Americas. Streamlining distribution in this way reduces lead times and adds flexibility to the system when demand is high.
3. More modes of transport
Truck driver shortages in the US are leading to bottlenecks at its major ports, including Los Angeles, and creating huge queues of container ships waiting to offload. It’s a similar story in the UK’s largest port of Felixstowe. But supply chains should never sleep! Logistics providers need to be multimodal – using rail, river, sea and road to provide seamless 24/7 capability.
4. More digitalisation
The US and UK’s lack of capacity at major ports shows how supply chain disruption must be improved by using digital tools. Through the compilation of shared data, it is now possible to create additional “virtual” capacity through embracing regional warehouse collaboration. Digital tools can also give greater flexibility to cargo owners on how they move their product from factory floor to the customer’s door – DP World’s SeaRates tool, for example, is an online platform that allows cargo owners to compare the best rates and closely monitor the progress of their shipment. And, of course, digital technology helps speed up and even automate customs clearance processes, moving goods out of ports faster.
5. More infrastructure
While digitalisation should be at the heart of the logistics industry’s efforts to counteract supply-chain disruption, there’s no escaping the need for investment in major physical infrastructure. The Suez Canal blockage earlier this year was a wake-up call that we are incredibly reliant on key infrastructure along just a few vital routes to keep cargo flowing around the world and the onus is on governments to invest in opening up new routes such as a second Suez or the Northern Transit Corridor as a matter of urgency. For me, it’s important that the industry also learn from the challenges now being faced by some of the major US ports, by building infrastructure with future demands firmly in mind.
Published by
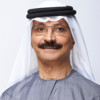
Source : Author – Sultan Ahmed Bin Sulayem ,Chairman & CEO of DP World, Chairman of Virgin Hyperloop
