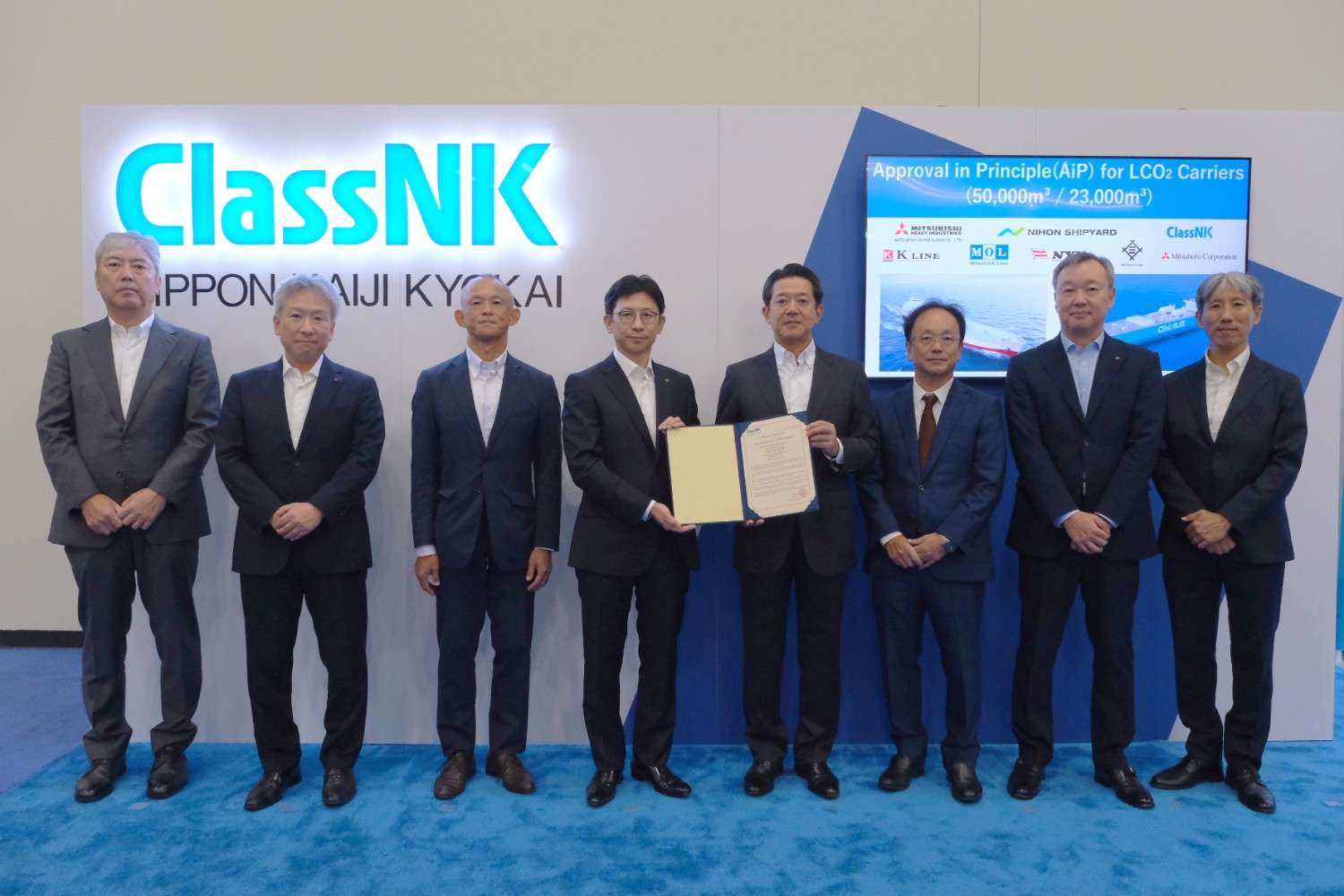
ClassNK issues Approval in Principle (AiP) for large liquefied CO2 carriers of 50,000 m³ and 23,000 m³
TOKYO : ClassNK has issued an Approval in Principle (AiP) for a design concept of large liquefied CO2 carriers of 50,000 m³ and 23,000 m³ jointly developed by Kawasaki Kisen Kaisha, Ltd., Mitsui O.S.K. Lines, Ltd., Nihon Shipyard Co., Ltd., Nippon Yusen Kabushiki Kaisha, Mitsui & Co., Ltd., Mitsubishi Corporation, and Mitsubishi Shipbuilding Co., Ltd. While Carbon dioxide Capture and Storage (CCS)*1 projects are proceeding worldwide, demand for liquefied CO2 carriers that transport CO2 from the capture site to the storage site is expected to expand. This AiP is a step toward standardizing hull designs, which is necessary in order to realize a sufficient number of liquefied CO2 carriers to meet such demand. The handover ceremony of AiP certificate was held at the ‘Gastech2024’ exhibition in Houston, USA.
ClassNK carried out a design review of the ships based on part N of its ‘Rules and Guidance for the Survey and Construction of Steel Ships’, which incorporates the IGC Code, an international code for the construction and equipment of ships carrying liquefied gases such as liquefied CO2 and LNG in bulk. ClassNK issued AiP after it was confirmed that the prescribed requirements were met.
This AiP includes a tank safety assessment process based on a fracture mechanics technique called Engineering Critical Assessment (ECA)*2 to omit post-weld heat treatment (PWHT)*3, which can be a bottleneck in tank manufacturing.
ClassNK will continually strive to contribute to advanced decarbonization initiatives through safety assessments and more.
*1 Carbon dioxide Capture and Storage (CCS)
Technology for separating and capturing CO2 from emissions and storage it in stable underground formations.
*2 Engineering Critical Assessment (ECA)
An evaluation method based on fracture mechanics to determine whether defects found in welds, etc. will cause phenomena such as collapse during the design life of a structure.
*3 Post Weld Heat Treatment (PWHT)
Heat treatment to reduce residual stress in the weld zone by reheating and holding the weld zone to approximately 600°C after welding. Generally, this treatment is performed in the heat treatment furnace, since it is reheated and maintained to a high temperature of about 600°C. When the tank is too large to be stored in the heat treatment furnace, the heat treatment is performed by local heating (using heater etc.), the heat treatment period may be increased as compared with the case where the heat treatment is performed in the heat treatment furnace, and there is concern that the tank may become a bottleneck in manufacturing.