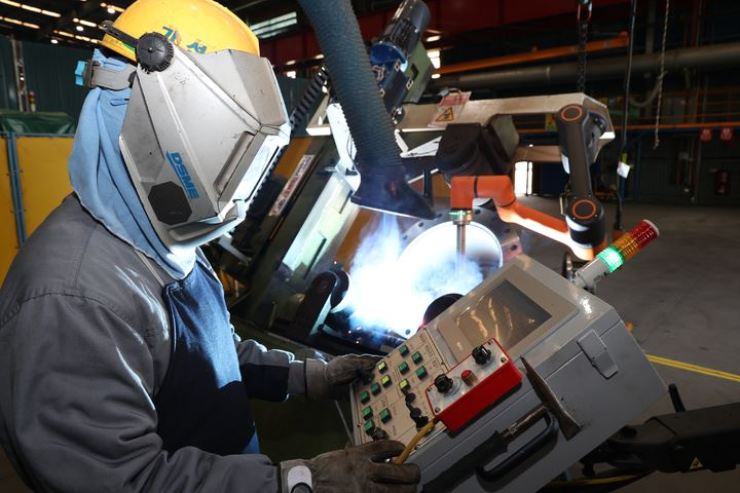
HD Hyundai says robots will be building ships in 2030
SEOUL : Fumes rise in the airy shipyard of HD Hyundai Samho’s panel factory, where blue-suited workers in welding masks assemble ship cells. Scattered throughout the space, robots tethered to vertical wires operate alongside human workers, delivering precise, smooth welding lines that surpass manual craftsmanship.
This is the everyday scene at the HD Hyundai Samho’s shipyard, which currently operates 54 collaborative robots on the scene. The dockyard possesses the most of HD Hyundai’s three shipbuilding affiliates, surpassing HD Hyundai Heavy Industries’ 26 and HD Hyundai Mipo’s 16.
The shipbuilding affiliate’s automation efforts align with its overreaching initiative to transform itself into a “smart shipyard” by 2030 — to develop a single platform that integrates all relevant data from vessel design, production and robot operations for seamless automation.
“Our company aims to create a ‘visible shipyard,’ which means making it clear who is doing what and how they are working,” said HD Hyundai Samho’s Ryu Sang-hun, Vice President of the Automation Innovation Center, told the Korea JoongAng Daily in an interview at its shipyard in Yeongam, South Jeolla, on Thursday.
“Why we do this? To guarantee quality. The goal is to track and improve the quality of work, such as welding, by using collaborative robots that gather real-time data. This data will help identify performance issues, ensure quality, and optimize productivity.”
AI is making its way into the shipbuilding industry. Though much of the industry is still powered manually, major Korean players like HD Hyundai, Samsung Heavy Industries and Hanwha Ocean see a more automated future. The center began deploying its robots in 2023, integrating hardware from Universal Robots, Rainbow Robotics and Neuromeka with proprietary software tailored to production.
“If someone is welding a steel plate, we don’t know who is doing it, under what conditions and how it is being done — the process is entirely reliant on individual skills. Now, the collaborative robots are collecting this data, and we can analyze to optimize the most cost-effective production process.”
Overall, HD Hyundai Samho believes its “intelligent autonomous shipyard,” if achieved in 2030, could both raise its productivity and reduce production time by 30 percent. That entails a facility in which robots independently descend, identify welding spots and carry out welding tasks without human aid.
The Automation Innovation Center aims to streamline its operations so effectively that rookie welders, after just one to two days of robot-assisted training, can contribute to constructing high-value liquefied natural gas LNG carriers. This is a significant reduction compared to the typical six-month training period required before welders are ready for on-site work.
Such a scenario is still quite a ways away, however, and five years ahead on the shipbuilder’s 2030 Future of Shipyard road map.
Workers still need to position the robots, entering required data with a touch pendant and manually initiating welding tasks. Both human and inanimate workers currently take an average of 10 to 15 minutes to weld per cell. However, workers achieve an average arc time of 25 percent, while robots, unaffected by fatigue, surpass 40 percent, according to the center.
Such “collaborative robots” are currently utilized in fewer than 10 percent of processes, and only for flat blocks, though they’ve been able to weld curved sections since July.
“The idea is for robots to seamlessly exchange CAD data and perform welding directly based on that information,” Ryu explained, referring to computer-aided design, adding that the company plans to invest in 12 additional units to support the initiative.
The center also plans to establish a dedicated training facility for testing robots, covering 357 square meters (3,843 square feet), which is set to be complete by March 2025.
“The center is not only responsible for advancing the technology, but managing the overall operations,” explained Hong Ji-woong, Senior Manager of Robot system development, during a press tour of the facility.
“The key to achieve successful automation is to consistently address issues and improve systems to ensure robots can be effectively applied even in challenging environments. For instance, workers who have earned certifications and operate the robots might lose their jobs when the robots break down. To maintain production, it is essential to minimize downtime and expand the capability to perform self-repairs on site.”
Hong showed cells done by humans and robots for comparison. Even to an untrained eye, the difference was striking: the robot-welded lines were clear and precise, while the human-welded lines appeared uneven and jagged.
The next Trump administration, with its tenacity to boost fossil fuels, is anticipated to lead to an upcycle for domestic shipbuilders, boosting order volume for tankers, LNG and LPG carriers.
However, the sector has long struggled with a shrinking, aging work force, as younger workers often leave for less physically demanding industries. The dwindling working population is being offset by foreign workers, as is the case in the Yeongam shipyard, where about 3,000 of the 15,000 workers originated from countries such as Vietnam, Nepal and Uzbekistan.
“There’s concern within the industry about passing on of critical on-site knowledge, especially with the loss of skilled engineers over the past decade,” Ryu said.
“Some workers are reluctant to share their expertise, fearing it could put their job security at risk, much like guarding a family recipe. This is where robots come to the scene. By collecting and applying data across machinery, we can bridge the gap between experienced workers and the next generation, ensuring that technical skills and knowledge are preserved and passed on.”