
Explained: Why the shipping container crisis will not end soon
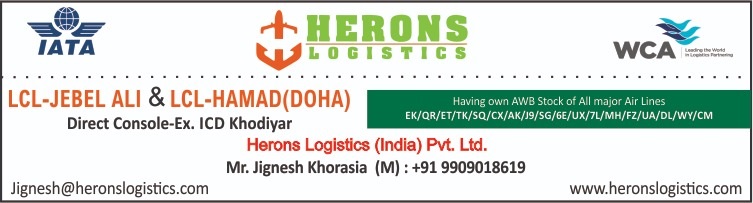
MUMBAI : Last weekend on a visit to the Jawaharlal Nehru Port in Navi Mumbai, India’s largest container handling port, Shipping and Ports Minister Shri Sarbananda Sonowal vowed to find an early solution to the ongoing shipping container shortage that had brought misery to both exporters and importers.
Around the same time, a record 87 container ships were waiting to enter the neighbouring ports of Long Beach and Los Angeles on the west coast of the United States. Most of those ships had started their journey from Asia, mostly China, loaded with perishable food items, consumer goods, gadgets, clothes, toys, machine parts and inputs for manufacturing plants.
It will be several days or even weeks before each of these ships gets a berth at the port to unload the containers, many more weeks before the boxes reach their final destination in the US and months before the empty ones are reloaded on a ship.
Ports on the east coast such as New York and New Jersey as also many European ones such as Rotterdam and Felixstowe are also facing congestion.
In the pre-COVID days and the early days of the pandemic, ships usually found a berth upon arriving at a port to unload their containers and get reloaded with new ones. The unloaded containers were promptly taken away by trucks to their destination. Thus, the movement and turnaround of containers were pretty efficient. The pandemic changed all that. There is a delay at every level. Making matters worse is the lack of space on ships for empty containers, which results in boxes piling up at container depots, ports and transhipment hubs such as Singapore and creating shortages in countries such as China and India.
There are no easy fixes to the problem of container shortages, notwithstanding the assurances given by Sonowal and fiscal relief announced by the Finance Ministry for a delay in the re-export of empty containers. Top shipping and ports industry executives and analysts have warned over the past few weeks that the crisis may persist for another year, even though the world’s largest container shipping companies such as Hapag-Lloyd and CMA CGM are augmenting their stock of containers. They have also given out contracts to build new container vessels.
However, increasing the stock of containers and improving their availability to exporters alone will not ease the crisis either in India or elsewhere in the world. The entire supply line is broken due to shortages of workers, missing truck drivers, contraction of the fleet on container ships and related reduction in the availability of slots on container ships and the imbalance in trade flows. Some vessels are undergoing refurbishment.
The ongoing crisis first emerged when households started spending their forced savings to buy goods from e-commerce platforms during the summer of 2020. The massive fiscal stimulus also buoyed consumption. Essentially, spending shifted from services to goods when some form of lockdown was in force. The spurt in demand caught importers and logistics service providers by surprise, as most of these goods had to be shipped from China, eastern and south-eastern nations, usually in containers.
The shortage of containers became acute in recent months when retailers in the US and other western countries started stocking up ahead of the holiday season. The pressure on the logistics networks rose when manufacturers advanced their import orders for raw materials and critical inputs to avoid disruptions to production cycles.
The container crisis will not ease till the factors that caused it are addressed.
First of all, the flow of empty containers back to exporting countries needs to be normalised. Currently, a large number of empty containers are stranded in inland depots, ports and adjoining empty patches of land in the US and Europe, as there aren’t enough vessels sailing back to Asia where these boxes are needed. Some others are parked at transhipment hubs across Asia, waiting for ships willing to do the short-haul trips within the region.
Shipping companies find moving stuffed boxes from east to west more lucrative, than hauling empties in the reverse direction. Transporting empty boxes is less profitable.
According to the Drewry World Container Index, spot rates in the east-bound routes is a fraction for those on ships sailing westward. For instance, the spot freight rate for 40 feet containers on the Shanghai-Los Angeles route was over $10,000 but under $1,300 in the reverse direction in the recent weeks. Similarly, it was $13,400 on the Shanghai-Rotterdam route and $1,600 in the reverse direction. With consumption still very strong in the US and Europe, it might be months before ships start accepting empty boxes.
Shortage of workers at ports and through the logistics network and missing truck drivers have also caused the piling up of containers, both stuffed and empty, at ports, warehouses and depots. Many others remain stacked on board, waiting for several days to enter ports, as ports can function efficiently only when the rest of the chain also moves containers rapidly.
The workforce at every level contracted when demand collapsed following the first wave of the pandemic. All facilities continue to grapple with labour shortages, slowing the entire chain of processes from unloading of containers, their movement to depots and warehouses and onward journey. Therefore, congestion continues at almost all large ports.
Thanks to the congestion, the idling of vessels have risen and exacerbated the shortage of ships that can go into the sea. The shortage of truck drivers for long haul trips had reached alarming proportions, so much that Moody Analytics described it as the weakest link in the supply chain.
Some relief can be expected in February when factories across China will shut down for the Chinese New Year celebration, slowing the flow of goods from that country. A lull in demand following the Christmas shopping across the US and Europe is also expected to ease congestion at the ports.
However, the resurgence in COVID-19 cases in many European countries could prolong the pain. For now, dozens of vessels waiting at ports to unload their cargo and exporters and shippers in India, China and elsewhere in Asia can only hope that disruptions due to the fresh breakout will be minimum.
The ongoing crisis first emerged when households started spending their forced savings to buy goods from e-commerce platforms during the summer of 2020. The massive fiscal stimulus also buoyed consumption. Essentially, spending shifted from services to goods when some form of lockdown was in force. The spurt in demand caught importers and logistics service providers by surprise, as most of these goods had to be shipped from China, eastern and south-eastern nations, usually in containers.
The shortage of containers became acute in recent months when retailers in the US and other western countries started stocking up ahead of the holiday season. The pressure on the logistics networks rose when manufacturers advanced their import orders for raw materials and critical inputs to avoid disruptions to production cycles.
The container crisis will not ease till the factors that caused it are addressed.
First of all, the flow of empty containers back to exporting countries needs to be normalised. Currently, a large number of empty containers are stranded in inland depots, ports and adjoining empty patches of land in the US and Europe, as there aren’t enough vessels sailing back to Asia where these boxes are needed. Some others are parked at transhipment hubs across Asia, waiting for ships willing to do the short-haul trips within the region.
Shipping companies find moving stuffed boxes from east to west more lucrative, than hauling empties in the reverse direction. Transporting empty boxes is less profitable.
According to the Drewry World Container Index, spot rates in the east-bound routes is a fraction for those on ships sailing westward. For instance, the spot freight rate for 40 feet containers on the Shanghai-Los Angeles route was over $10,000 but under $1,300 in the reverse direction in the recent weeks. Similarly, it was $13,400 on the Shanghai-Rotterdam route and $1,600 in the reverse direction. With consumption still very strong in the US and Europe, it might be months before ships start accepting empty boxes.
Shortage of workers at ports and through the logistics network and missing truck drivers have also caused the piling up of containers, both stuffed and empty, at ports, warehouses and depots. Many others remain stacked on board, waiting for several days to enter ports, as ports can function efficiently only when the rest of the chain also moves containers rapidly.
The workforce at every level contracted when demand collapsed following the first wave of the pandemic. All facilities continue to grapple with labour shortages, slowing the entire chain of processes from unloading of containers, their movement to depots and warehouses and onward journey. Therefore, congestion continues at almost all large ports.
Thanks to the congestion, the idling of vessels have risen and exacerbated the shortage of ships that can go into the sea. The shortage of truck drivers for long haul trips had reached alarming proportions, so much that Moody Analytics described it as the weakest link in the supply chain.
Some relief can be expected in February when factories across China will shut down for the Chinese New Year celebration, slowing the flow of goods from that country. A lull in demand following the Christmas shopping across the US and Europe is also expected to ease congestion at the ports.
However, the resurgence in COVID-19 cases in many European countries could prolong the pain. For now, dozens of vessels waiting at ports to unload their cargo and exporters and shippers in India, China and elsewhere in Asia can only hope that disruptions due to the fresh breakout will be minimum.