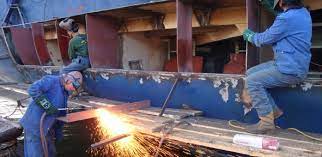
Durban’s ship repair skills praised after 96.5 tonnes of steel used to fix Indian vessel
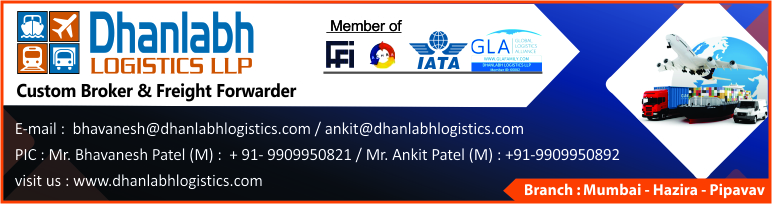
DURBAN : The ship repair skills and ingenuity of the Durban based Sandock Austral Shipyards (SAS) were put to its full test when the team undertook the repair of the bow of the Bulk Carrier, the Vishva Bandhan during which a total of 96.5 Tonnes of steel was used.
The repair has earned praise as much welding was done in the water – before being sent to the drydock.
In addition, the intricate and complex steelwork which had to be shaped and formed prior to fitment was done in-house.
The Vishva Bandhan is owned and operated by the Shipping Corporation of India and is a Bulk Carrier that was built in 2011.
On May 18, 2021, the vessel which sails under the flag of India was arriving in the Port of Beira, Mozambique, when it was involved in a bow-to-bow collision with a smaller container vessel.
The damage to the bow area reportedly occurred whilst the vessel was manoeuvring and under pilotage from the outer anchorage area to the loading coal berth.
The collision reportedly occurred in the navigation channel and was blamed on poor weather conditions at the time.
So extensive was the damage that the owners of the ship immediately contacted SAS. The damage was assessed upon its arrival in Durban.
Charles Maher, the Head of Marketing and Head of Project Portfolio Management Office (PPMO) at SAS said that the vessel had unfortunately also sustained underwater damage and it was decided that the best course of action was for the vessel to sail to Durban where the vessel could be docked and effectively repaired.
Maher said the project involved devising an innovative, fast, and cost-effective repair strategy to minimise the bulker’s time out of service.
The time taken by the shipyard to complete the project is critical, as every day that it is out of commission results in lost revenue. As usual with these types of collisions, the damage was more extensive than initially envisaged so it was critical that we worked around the clock to ensure no additional time was needed,” he said.
The SAS Project Management Team devised a repair in-situ as the original build plans were not available to allow pre-fabrication and the time allowance would not be justified for the fabrication on arrival.
The SAS team immediately set about the de-construction phase in-water while they waited for the Dry-Dock to become available.
Approximately 70 Tonnes were dismantled, and 50 Tonnes fitted and welded alongside in a period of 14 days which also saved the owners unnecessary dry-docking costs.
“Thanks to SAS’s shipbuilding activities all the steel plates were available and were able to be cut, prepped and shaped by SAS shipbuilding facilities. Every single plate with thicknesses up to 25mm had to be shaped and formed prior to fitment and all of it was done in-house,” Maher said.
In fact, Maher added, SAS even carries out the shaping and forming of steel plates for other ship repairers in the port due to the confidence and rapid turnaround times that cannot be matched.
The vessel was placed in the dry-dock for an additional 21 days to complete the repairs which eventually totaled 96.5 Tonnes of steel as well as a full coating system.
“The owners were very impressed with the efficiency despite COVID restrictions at the time and the vessel was able to continue to her loading port after undocking,” he said.
Source : IOL
